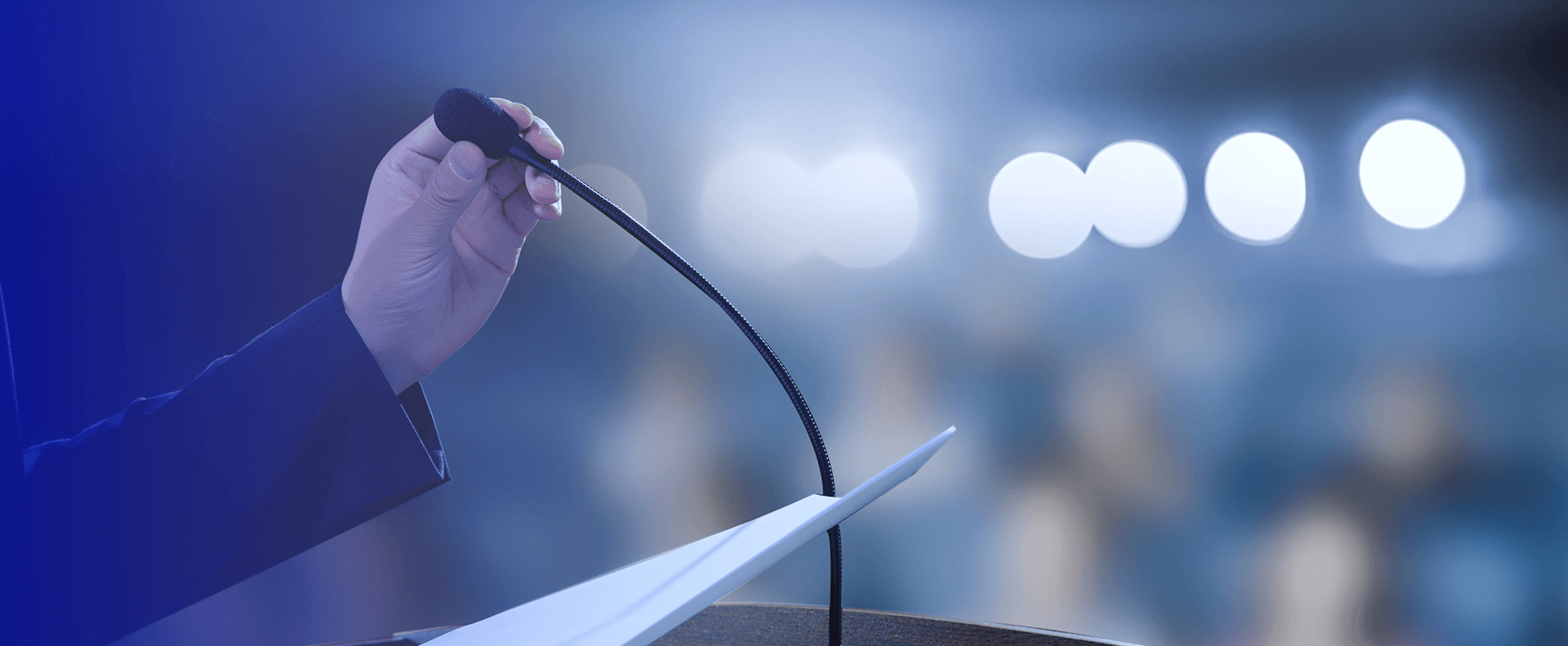
鑄造是現(xiàn)代機械制造工業(yè)的基礎工藝之一,具有成本低廉、一次成形以及可以制造復雜結構大型件等優(yōu)點,被廣泛應用于汽車零部件、機械制造、電子、醫(yī)療器械、鐘表儀器、五金產(chǎn)品、航空航天等工業(yè)生產(chǎn)的眾多領域。X射線無損檢測由于可避免材料浪費和提高生產(chǎn)效率,成為鑄件缺陷檢測的主要方法。
氣孔是精密鑄造的常見缺陷之一。氣孔是指精密鑄件個別位置出現(xiàn)光滑孔眼缺陷。通常在機加工后才能發(fā)現(xiàn)氣孔。鑄件中產(chǎn)生氣孔會破壞金屬的連續(xù)性;承載的有效面積較少;氣孔附近易引起應力集中,使機械性能下降;彌散孔也會導致氣密性下降。
在大多數(shù)情況下,鑄件中產(chǎn)生氣孔主要是因為精密鑄模殼未完全烘烤。澆注鋼水時,在模具殼內(nèi)產(chǎn)生大量的氣體,不能順暢地排出,然后侵入到金屬水中而形成氣孔。也有進行制殼工藝或殼形材料的原因。殼體的氣體滲透性太差,并且空腔中的氣體難以排出,并且其進入熔融金屬中形成孔。由于在澆注過程中吸入鋼水的空氣無法排出而造成鑄孔。
形成鑄件的氣體侵入孔是因為積聚在砂料表面上的氣體滲透到液態(tài)金屬中,并且鑄模材料包含各種添加劑,例如水分和粘結劑。這些孔大部分位于表面附近,具有較大的大小,橢圓形或梨形,并且孔的內(nèi)表面被氧化。在澆注過程中,一部分水蒸氣從分型表面的排氣孔排出,另一部分聚集在表面上,形成高壓中心點。當氣壓上升并融化到金屬中時,其中一部分會從熔融金屬中逸出,其余的會在鑄件內(nèi)部形成孔洞。
鑄件內(nèi)部的氣孔無法通過表面觀察檢測出缺陷產(chǎn)品,需要進行無損檢測才能確定其質(zhì)量。通過各種鑄造方法獲得的鑄件的精度不同,初始投資和生產(chǎn)率也不一致,最終經(jīng)濟效益也不同。因此,為了變得更多,更快,更好和更便宜,有必要不斷改進生產(chǎn)工藝,以控制鑄件質(zhì)量,合理選擇鑄件合金和鑄件結構。
在生產(chǎn)過程中,鑄件如何減少氣孔的出現(xiàn)?在精密鑄造條件允許的情況下,在結構復雜的鑄件較高部位設置排氣孔;在設計澆注系統(tǒng)時,應充分考慮殼的排氣要求;殼的烘烤溫度和時間應合理,保溫時間也應足夠;脫蠟時應徹底清除蠟;適當減小鋼包噴嘴與澆口杯之間的距離,澆注速度應均勻,以確保鋼水平穩(wěn)地充滿型腔,并盡可能少地將鋼水中的空氣吸入型腔;鋼水可以順暢地排出。
鑄件質(zhì)量的控制除了采取一定的預防措施外也需要選用合適的質(zhì)量檢測設備。X射線鑄件氣孔檢測設備十分適用于鑄件內(nèi)部缺陷的檢測,X射線能夠穿透鑄件,對鑄件內(nèi)部進行實時成像,通過軟件缺陷自動識別系統(tǒng),直接在檢測圖像上標記缺陷位置和大小,檢測效果直觀且不會破壞鑄件本身,是一種有效的無損檢測方式。
以上就是《X射線無損探傷用于鑄件質(zhì)量檢測分析》的內(nèi)容介紹,由于鑄造工藝過程復雜,影響鑄件質(zhì)量的因素很多。原材料控制不嚴、工藝方案不合理、模具結構設計不合理、生產(chǎn)操作不當?shù)榷紩硅T件產(chǎn)生各種缺陷,常見缺陷有夾雜、氣泡/氣孔、疏松和裂紋等。為保證鑄件質(zhì)量及節(jié)省成本,在生產(chǎn)流程的早期階段及時檢測出缺陷是很必要的。
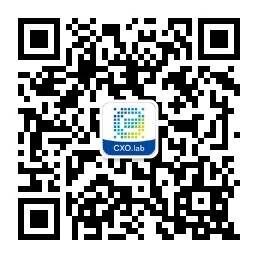